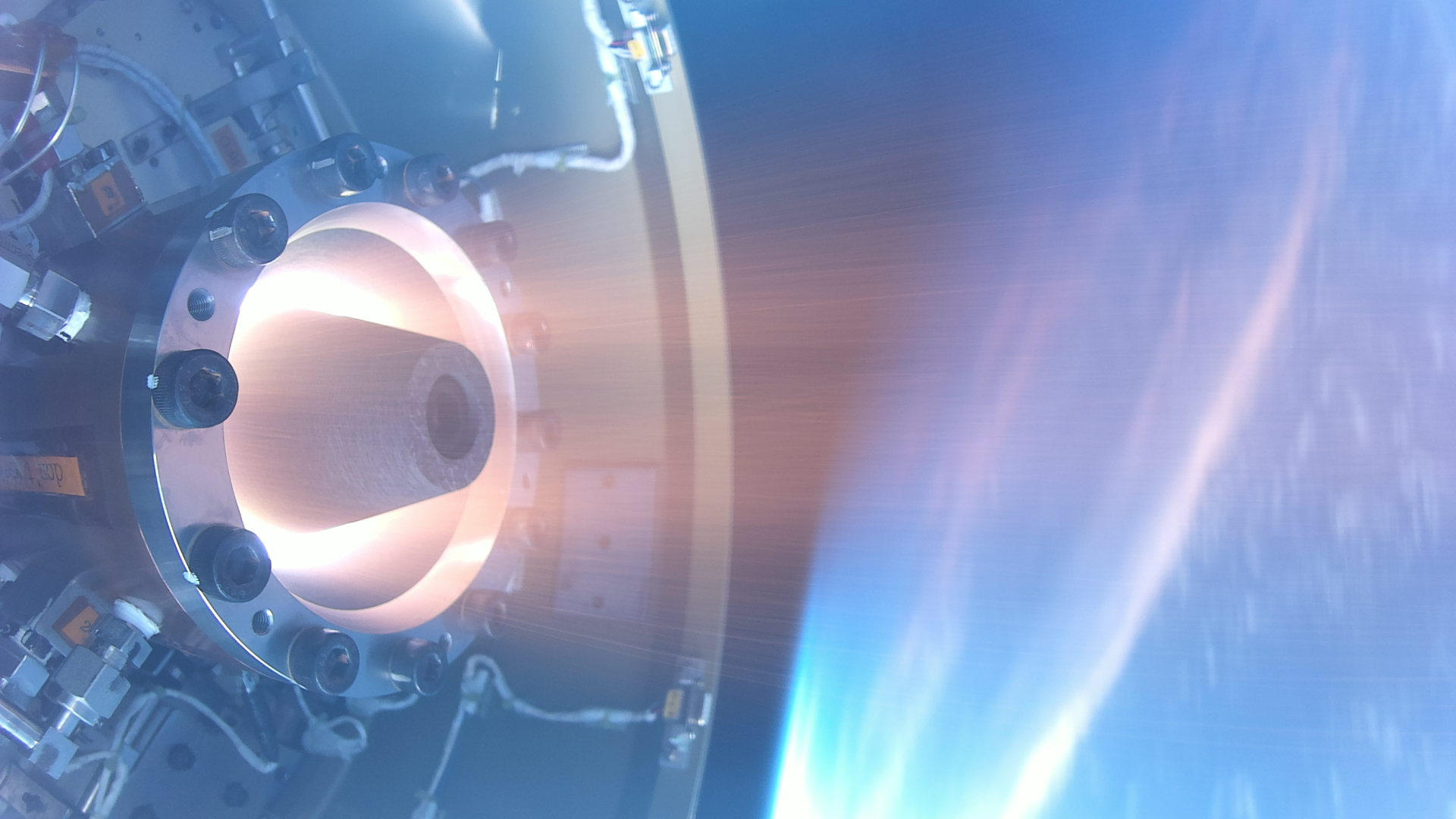
The world’s first space flight for the rotating detonation engine, and a glimpse at a new sample return capsule
In the early hours of July 27 last year, the sounding rocket S-520-31 shot into the sky from JAXA’s Uchinoura Space Center. As with all sounding rockets, the flight was brief and the 8m long rocket dropped into the sea eight minutes after launch. Splashing down alongside the rocket were records of the flight on a chip embedded in JAXA’s newest re-entry capsule. That data would reveal that for six seconds above the Earth, the S-520-31 was powered by a new type of rocket engine in the first successful space flight demonstration in the world.

The S-520 series sounding rocket is usually propelled by hydroxyl-terminated polybutadiene (HTPB), ammonium perchlorate (AP), and aluminum (Al): a solid rocket propellant where the fuel and oxidising agent is blended together. When ignited, the fuel vaporises and combusts to create a high temperature and pressure exhaust gas which is channelled through a nozzle to generate thrust.
The S-520-31 launched powered with the usual HTPB/AP/Al solid fuel. But as combustion finished and this first stage fell away, the rocket switched to a second source of power: a Rotating Detonation Engine System (RDE).
“Detonation” refers to when the flame front in the ignited fuel-oxidizer mixture moves so fast that it surpasses the speed of sound. Normally, the expansion of burned gases behind the on-coming flame would cause the unburned fuel-oxidizer mixture to move outwards. But the progression of the flame front during a detonation is so rapid that there is no time for the unburned mixture to get out of the way. Instead, the pressure and temperature leap upwards while the volume rapidly decreases. The is referred to as a detonation shock wave.
Burning the fuel-oxidizer mixture before it expands leads to fast and efficient combustion, as the denser fuel-oxidizer mixture can be burned rapidly. However, the detonation wave would usually shoot out the rocket engine with the combustion products and have to be restarted.
But continuously restarting the igniting detonation wave is avoided in a Rotating Detonation Engine System by confining the wave to travel around an open-ended cylindrical chamber. Travelling in a circle, the wave continuously ignites fresh fuel-oxidizer mixture as it is fed into the chamber. As the detonation wave repeatedly slams through the fuel on its circular path, rapid combustion occurs and the resulting products expand upwards and accelerate out the chamber end to generate thrust.
Such a system—explains Professor Kasahara Jiro from Nagoya University—could considerably reduce the size of the rocket engine. With rapid burning and with no need to compress the expanding fuel, the combustion chamber in a detonation engine can be much smaller. It might even be possible to remove this chamber entirely, suggests Kasahara, and embed the denotation system inside the fuel tanks or another part of the rocket structure.
Detonation combustion can also result in much larger pressure and temperature leaps that can greatly increase the efficiency compared to that of a conventional rocket engine. However, Kasahara notes that this remains a topic of global research and current designs do not yet achieve vastly higher pressure increases. He feels that a first important application for the rotating detonation system will be in conjunction with traditional rocket engines, acting as an additional boost in power. In the case of the S-520-31 sounding rocket, the RDE acted as a second stage of propulsion. For larger launch vehicles such as JAXA’s Epsilon rocket or the H3, the RDE could be use for the final orbital adjustments (kick stage). However, this could change in the future.
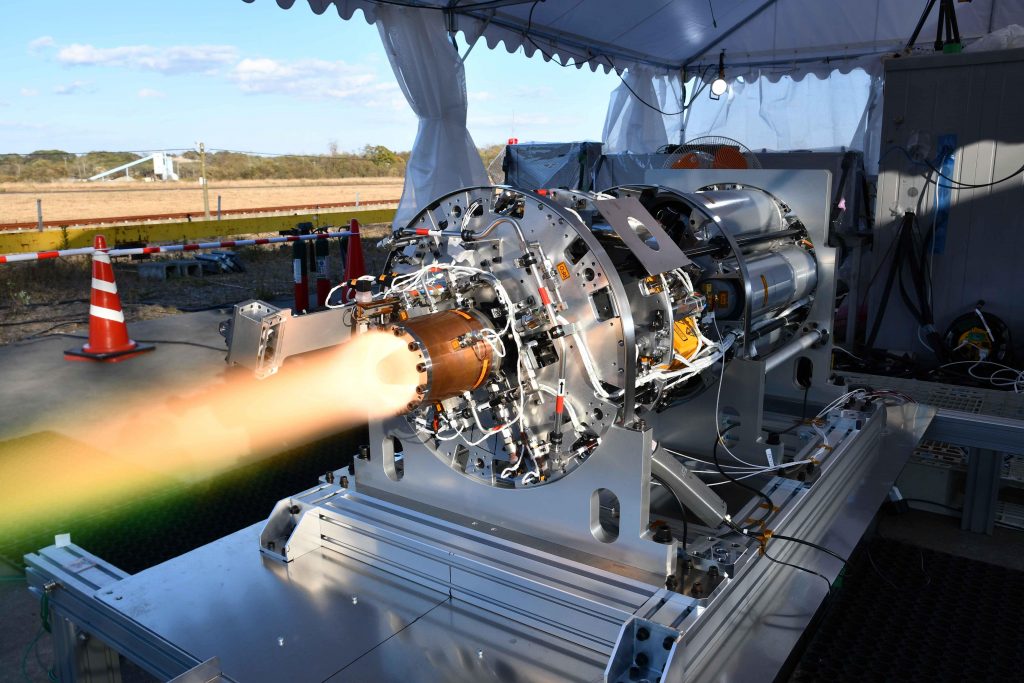
“In the future, there is a very high possibility that detonation engines will also be used for the first and second stage engines,” says Kasahara. “Because of the light weight and simple structure, I believe that once this trend occurs, there will be no turning back. The change will be similar to the change from cathode-ray tube televisions to LCD televisions, and I don’t think it will be reversible.”
Kasahara envisages one of the most important uses will be in chemical propulsion in deep space exploration, where the mass requirements for the spacecraft are particularly stringent. The high weight cost of spacecraft fuel is why JAXA have focussed on ion engine technology to power long interplanetary journeys for missions such as Hayabusa2. However, ion engines gather speed slowly and are unsuitable where quick manoeuvres are necessary, such as close to planetary bodies. For this, lightening the load for chemical propulsion would be game changing.
In the S-520-31 flight, the RDE achieved 500 N of thrust. While this looks sizeable, it remains a small push compared to even medium-class rocket engines where each stage provides millions of newtons of force. This problem can be relatively easily resolved by using a grid of RDE thrusters. Due to the speed of detonation combustion, a layout of 100 x 100 RDE thrusters is obtainable, which would provide of order 5 million newtons of force. This is more than double the force provided by the first stage of the Epsilon rocket.

The exact details of the RDE flight (digital video, data of engine pressure and vibration) were recorded in a chip onboard the sounding rocket, embedded in JAXA’s newest re-entry capsule. A re-entry capsule is designed to protect its cargo during the descent through the Earth’s atmosphere, where the rapid drop causes the surrounding air to shock heat to thousands of degrees. In December 2020, the Hayabusa2 Sample Return Capsule blazed across the Australian night sky as it brought the sample from asteroid Ryugu home to Earth. But despite the fireball exterior, conditions within the capsule remained at room temperature.
Although the new capsule has the same objective as technology for entry, descent and landing—explains Associate Professor Yamada Kazuhiko in the Department of Space Flight Systems at ISAS—it utilises a very different technical concept.
The new design is the “Reentry and recovery module with deployable Aeroshell Technology for Sounding rocket experiment” or RATS. While the Hayabusa2 capsule had a rigid aeroshell to protect against the heat, RATS has a deployable aeroshell made of flexible material that is inflated by injecting gas into an inflatable ring. This provides a large area while significantly reducing the weight of the capsule, allowing descent to be slowed by even a low density atmosphere. A slower descent reduces the heating from the surrounding atmosphere, avoids the need for a parachute and can also float in water using the same inflatable ring.

“These unique characteristic could allow us to develop a simple and innovative re-entry and recovery system,” says Yamada. “RATS in the S-520-31 demonstrated that this atmospheric entry technology is suitable for a recovery system in sounding rocket experiments. In the future, this technology may also be used for planetary probes visiting planets with an atmosphere, such as Mars or Venus.”
RATS’ deployable aeroshell has been in development since 2000 with a team from ISAS, The University of Tokyo and several other institutes. Tests for aeroshell began in a wind tunnel, before drop tests from scientific balloons and then sounding rockets. The S-520-31 launch was the first time the capsule was put to practical use.
While the sounding rocket flight may have been over in minutes, the practical applications demonstrated with RDE and RATS point to an extremely long future in space exploration!
Further Information:
ISAS web release (in Japanese)
Nagoya University press release
Nagoya University Propulsion and Energy System Engineering Research Group
Hayabusa2 website